Case Study
Innovative dynamometer design
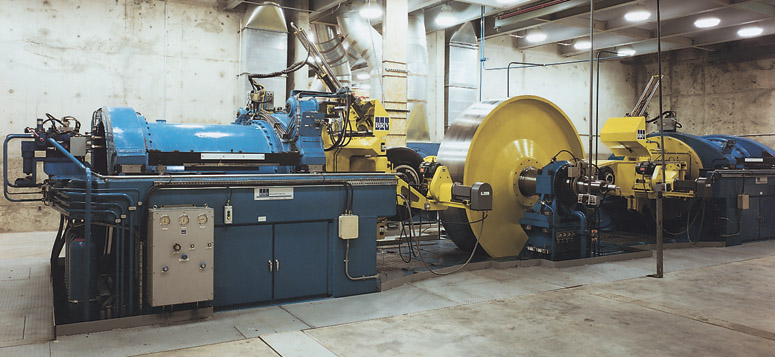
Design & Projects
Limited provides an
engineering design and project management service that specialises in providing solutions
to novel and complex engineering challenges. Typical of the type of work routinely
undertaken with the aid of LUSAS Analyst is an innovative design for a new type
of dynamometer - intended for use in testing aircraft tyres and brakes in the USA.
With conventional dynamometers, test
wheels run on the outside of the roadwheel. However, in this design brief, it was proposed
to run the test wheel inside the roadwheel flange, with the benefit of allowing surfacing
to be applied to the inside of the flange to give a more realistic testing arrangement.
Test wheel tyre sizes of 18-56" diameter and having widths varying between 6-25"
had to be accommodated. Recommended design ratios for test and roadwheel diameters
resulted in a dynamometer internal flange diameter of 172" being required to give the
correct amount of tyre contact. Tyre loads of 150,000 lbf acting vertically and 30,000 lbf
acting normal to the wheel's plane of rotation had to be applied to the LUSAS model and a
roadwheel speed of 350 mph was to be used to arrive at maximum in-service stresses.
Because of the type of analysis required, the use of LUSAS was considered essential in
order to achieve a credible and cost-effective solution
From initial studies, hoop stresses in
the flange were found to exceed 400MPa. Since centrifugal stresses accounted for the
majority, there was little scope for refining a conventional design so this led to the
development of a scheme to add a shrunken rim to the flange of the roadwheel, to induce
compressive stresses in the stationary state. The profile of this rim allowed material of
a higher strength than the roadwheel to be used.
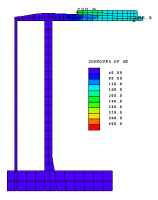
|
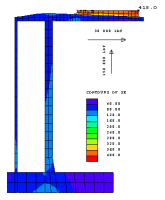
|
Stresses from fitting shrunken rim |
Stresses from tyre loading and 350 mph roadwheel speed |
LUSAS was used to investigate the effects of varying the
relative thicknesses of the flange and rim, together with looking at changes in the
interference fit. As the roadwheel was basically asymmetric, the Fourier analysis
capability of LUSAS was used. This allowed small changes to be incorporated and
re-analysed rapidly. The effectiveness of this approach was tested against a simpler model
analysed both symmetrically and as a full 3D model. An optimum loading pattern was found
to simulate tyre landing impact and used throughout the remaining study. The innovative
dynamometer design was judged a success with a good balance being achieved between the
initial compressive stresses and the maximum operational tensile stresses. From the
results obtained an additional fatigue assessment was done to evaluate any potential
fatigue problems.
"This
project is typical of the work we undertake. We specialise in undertaking novel
engineering challenges so we need analysis software that provides reliable answers for any
type of analysis problem. LUSAS Analyst meets our needs in this respect and helps
to enhance our in-house design skills in a very cost-effective way".
Bill Coleman, Director at Design & Projects
Other LUSAS Analyst case
studies:
|