Case Study
Estimating
Impact Damage in Honeycomb Sandwich Panels
Composite sandwich construction is used increasingly for aerospace
applications in components such as the trailing-edge wedges of aircraft flaps. However,
sandwich structures are generally poor at resisting impact damage. The Centre for Polymer and
Composites Research at the University of Auckland used LUSAS Composite to
develop a damage material model that will simulate core failure in sandwich panels under a
range of impact loading.
On aircraft flaps, low speed impacts can occur from tool drops, hail, or
debris thrown up from runways. High speed impacts can also occur with low mass bodies such
as birds. Two different numerical simulations using the developed damage material model
have been performed to give a comparative assessment of both types of impact with
experimental testing.
The damage
material model is based upon a combination of elastic and inelastic strain accumulation
together with degradation of the modulus matrix. It requires an initial damage threshold,
the gradient of the damage function, and the maximum permissible value of damage to be
defined. From experimental data, the reduction in stiffness was found to be 60% for
typical Nomex honeycomb, giving a modulus ratio of 40%. The damage material model was
embedded within an axisymmetric, explicit dynamic analysis, additionally taking account of
finite strain and large deformation behaviour. |
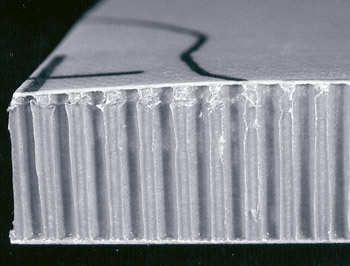
|
In the soft body experiment, a rubber membrane filled with water was
used as the impact projectile. To model this, an isotropic, elastic material with a low
Young's modulus and a Poisson's ratio close to 0.5 was defined to allow constant volume
deformation. Clamps on the panel boundary were represented by appropriate supports in the
LUSAS model. Slidelines automatically handled the contact between the impacting body and
the sandwich, and also tied the components of the sandwich model together. In all, 35,706
time increments over a total elapsed time of 6.44ms modelled the impact event.
During a soft body impact the projectile deforms over the surface of the
sandwich causing a shallow, large plan area defect to develop and remain in the sandwich.
The diameter and depth of the internal core damage predicted by LUSAS from this event
compared very well with the experimental results. By plotting the contours of damage using
LUSAS the extent of honeycomb crushing in the core of the sandwich could be easily seen.
Download an AVI file of the soft
body impact (1.5Mb) |
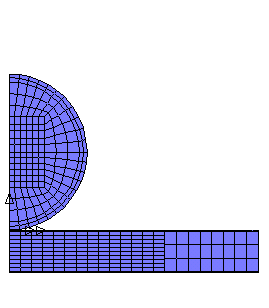
|
Overall, the analysis of soft impacts using the damage material model
showed good correlation with experimental results in terms of the damage diameter and core
crushing depth. The permanent deformation calculated using the damage model was found to
be about twice that of the experimental panels. A combination of time dependant recovery
and the sectioning of the panels to make measurements may account for this. The LUSAS
model does, however, provide a value for the maximum deformation in the panel at peak
impact.
In a hard body impact study using the same damage material
model, a projectile impacting with a velocity of 15.3ms-1 normal to the sandwich surface
was analysed using 28,000 time increments, over a total elapsed time of 2.4ms. The extent
of the core crushing is shown by the arrows on the accomanying diagram and the left-hand
boundary of core damage is shown by the circled area.
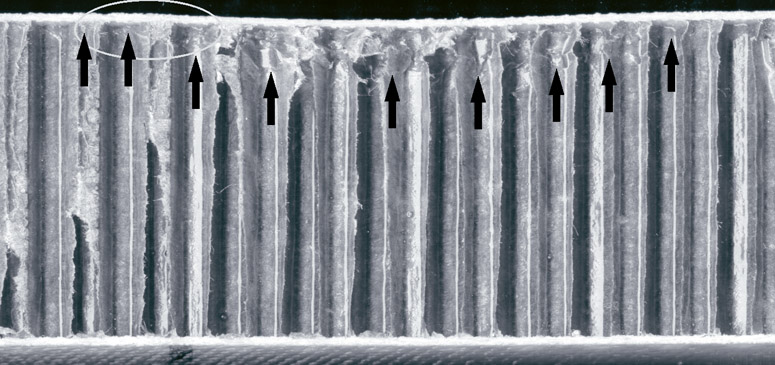
Results from this LUSAS analysis appear to underestimate the diameter of internal
core damage. This underestimate occurs because the model, currently, does not sufficiently
calculate low level core damage in a thin layer at the defect boundary that occurs in the
experimental case. A component of the lower numerical estimate may also be attributed to
differences in modelling the damage formation in a continuum as opposed to a cellular
structure that exhibits discrete 3mm jumps in the size of damage. In this instance the
damage is underestimated by approximately three cell diameters.
More detailed information on this case study |
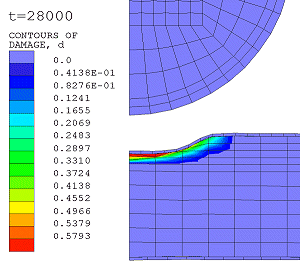
|
Other LUSAS Composite case
studies:
|
|
Software Information
|