User Area
Software Release History - Version 19
Version
19.1 | Version
19.0
New Facilities and Improvements
in LUSAS Version 19.1
V19.1-3 made available on 8 February 2022
This is an error
fix release.
V19.1-2 made available on 29 June 2021
This is a major
release of new facilitites, enhancements and change requests.
New software product: LNG Tank Analysis
and Design System
- The
'LUSAS LNG Tank Analysis and Design System' is a licensed
software product that allows engineers to automatically create a
range of 2D and 3D
finite element models of full containment circular tanks from
user-defined parameters. Using these models, a range of analyses
can be performed and optional design checks carried out for
specified load combinations and supported design codes.
Steel Frame Design
- The
Steel
Frame Design software option has been extended to include
design checks for BS5400-3:2000
Concrete Creep and Shrinkage
- The
range of concrete creep and shrinkage material models has been
extended to include those for Chinese
code JTG 3362-2018 and fib Model
Code 2010.
- For
Codes of Practice that include suitable clauses, material
properties and creep/shrinkage behaviours can be adjusted
according to a prevailing temperature during the service life of
the structure. This includes CEB-FIP Model Code 1990, fib Model
Code 2010, and JTG 3362-2018.
- The
age
of structural elements at the time of their activation can now be
calculated with adjustment for temperature during curing.
Prestress
- Time
dependent prestress capabilities have been extended to include
those for Chinese
code JTG 3362-2018 and fib Model
Code 2010.
Vehicle Load Optimisation
- The
Vehicle
Load Optimisation facility has been extended to support more
brdige assessment codes and now includes optimised loading and custom vehicles for
United States of America
AASHTO
MBE Section 6A (LRFR) and United Kingdom CS
458 rev 0 with ALL Model 1.
RC Frame Design
- RC
Frame design now allows the direction of the neutral axis to
be defined for uniaxial bending as part of defining the RC design
attributes for all supported
design codes.
Design combinations
- The
Design
combinations facility, which assigns LUSAS loadcases, envelopes or
basic combinations to predefined load types for a supported design
code, now supports CS 454, IRC: 6-2017, EN1990
for Railway Bridges and Footbridges - for Recommended Values and
Irish, and UK National Annexes, and EN1990 for Highways Bridges
and Footbridges for the Italian National Annex.
- The
design combinations implementation for Highway Bridges for EN1990
for Recommended Values, Irish, and UK National Annexes has been
extended to include 'Persistent Combination Set C'.
Cursor-based box selections
- A
right-to-left definition of box extents can be optionally set to
select all features crossed by the selection box (as often used by
CAD software), rather than include only those items wholly inside
the selection box.
Thick beam warping
- For
thick beams that support warping, torsional
end conditions can now be defined.
LUSAS Teaching and Training version limits
increased
- The
Teaching and Training version of LUSAS, which restricts the size
of model that can be solved, now has the following increased
limits:
Nodes
|
Points
|
Elements
|
Degrees
of Freedom
|
Loadcases
|
1000
|
200
|
500
|
3000
|
20
|
File export
- Export
of LUSAS model data to a Visual
Basic Script file is now provided.
Improved exporting of results data for use by
the Composite Deck Designer (PontiEC4)
- Exporting
of results can now be used with 2D grillage or 3D analysis models
made from beams, shells, or a combination of those element types.
- Composite
Design Member details are now used when exporting force and moment
results data for use in carrying out design checks by the
Composite Deck Designer (PontiEC4) software option. As a
consequence, beam/shell slice resultants can now also be exported.
For more
information see Composite
Bridge Deck Design (PontiEC4)
Associated model data
- The
'Associated Model Data' folder, that holds files created in the
course of a building a model and running an analysis, is now named
'LusasFiles32' for a 32-bit installation.
- The
previous ability to specify alternative locations of files that
are created in the course of building a model and running the
various analyses associated with it, as specified via the LUSAS
configuration utility, has been removed.
Restricted 64-bit LUSAS Modeller (Beta)
- Version
19.1 offers a new restricted 64-bit beta version of Modeller that
should only be used if advised to do so by LUSAS Technical
Support. Users are recommended to keep using 32-bit Modeller as
geometry cannot be edited in this beta version.
New Facilities and Improvements
in LUSAS Version 19.0
Release history
V19.0-3 made available on 3 January 2020
This is an error
fix release to correct an urgent software issue preventing the loading
of any results file generated since midnight 1st January 2021 into
LUSAS Modeller.
Other error fixes and
change requests are included.
V19.0-2 made available on 27 July 2020
This is a major release
of new facilitites, enhancements and change requests
In summary:
- Steel / Composite Bridge Wizard introduced for quick and easy modelling of slab-on-beam composite I-girder bridges.
- Composite Bridge Deck design introduced for AASHTO LRFD 8th Edition.
- Steel Frame design has been extended to include AISC-360 and GB50017.
- Reinforced Concrete frame design extended to include AASHTO 8th Edition, AS5100.5-2017, IRC:112-2011 and CSA S6-14.
- Vehicle load optimisation has been extended to include IRC:6-2017.
- Geotechnical modelling capabilities extended to include additional Ko models, Phi-c reduction, drained and undrained conditions, and a Hoek-Brown material model.
- Bridge deck (grillage) attributes introduced for slab, and girder with top slab modelling of grillages.
- Bridge deck temperature and shrinkage profile loading.
- General variation of temperature or strain through-section
- Generate influences from beam / shell resultants and inspection locations.
- Model view "orientation cube" introduced.
- Branched analyses introduced.
- Access to Fast and Frontal Solvers provided.
- Direct Method Influence analysis improvements
- Rail Track Analysis enhancements.
- Slice resultants improvements.
- Results averaging speed-up.
- New and updated worked examples.
New facilities and improvements in more detail:
Steel/Composite Bridge
Modelling
Composite Bridge Deck Design
Steel Frame Design
Reinforced Concrete Frame
Design
- RC
frame design software option now supports:
- AASHTO
8th Ed. (USA)
- AS5100.5-2017
(Australia)
- IRC:112-2011
(India)
- CSA
S6-14 (Canada)
Reinforced Concrete Slab
Design
Vehicle Load Optimisation
|
Geotechnical
General modelling, analysis
and results improvements
General
New and updated worked
examples
|
Steel
/ Composite Bridge Modelling Wizard
The Steel Composite
Bridge Wizard generates the model geometry and corresponding mesh,
geometric, material, support and local coordinate attributes for
models of slab-on-beam composite I-girder bridges where the slab and
web are modelled with shell elements and the top and bottom flanges,
web stiffeners and bracing are modelled using beam elements.
Models can be defined
that accommodate:
- Straight
or curved decks of constant radius.
- An
arbitrary skew, where a skew can additionally be set per support
and interpolated across the spans.
- Any
number of spans and supports.
- Square
and skew bracing.
- Transverse
stiffeners.
- Design
utilities for design checking against supported design codes.
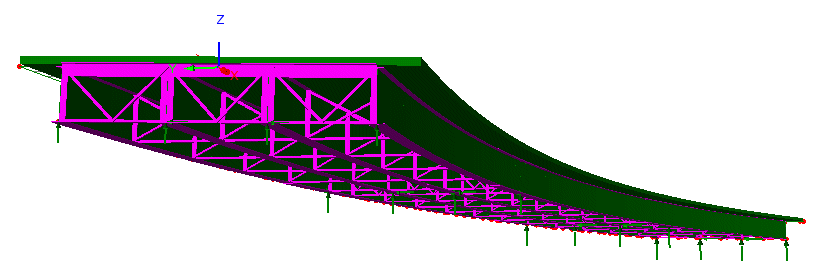
|
Example
of a curved multi-span steel composite bridge deck with
bracing created by the wizard
|
Composite
Bridge Deck Design
The Composite Bridge
Deck Design software option can be used with new or existing bridge models
for software licences that support this facility. It is for use with
2D Grillage/Plate and 3D element model types. When used with LUSAS
Bridge LT only 3D beam and 2D grillage models are permitted.
The Composite Bridge Deck Design option provides a consistent approach to design, regardless of the analysis approach adopted, using slice resultants to calculate design forces. This allows an analysis model to be created without having to define design details initially. It allows for the complexity of the analysis model to be increased without changing the design data, and also permits a number of changes to be made to the design information to see what the effect of a particular change would be, without having to change or solve the analysis model each time.
The following
steps are required to carry out a composite bridge deck design check:
- Create a model of the
bridge deck by using the Steel
Composite Bridge Wizard, or by using the grillage
wizard, or by manually creating an appropriate model, and solve it to obtain results.
- Define a composite
bridge deck design member for each girder (simple spans) or
series of girders (continuous spans) of interest in the model.
- Specify the design code
to be used by selecting the Design> Composite Deck
Design menu item.
- Define a results
utility This identifies the design members for which
calculations are required and brings together the loadcases /
combinations appropriate to the various limit state checks.
- View the results in
tabular format, and optionally add selected results to a model
report.
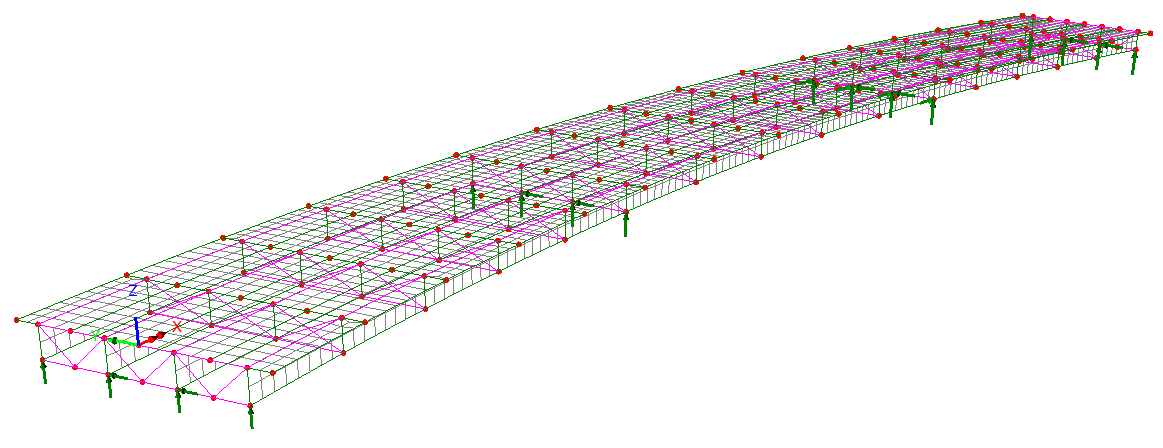
Design codes supported
The following design code is currently
supported:
- AASHTO
LRFD 8th Edition. (USA) - AASHTO LRFD Bridge Design
Specifications 8th edition, American Association of State Highway
and Transportation Officials 2017.
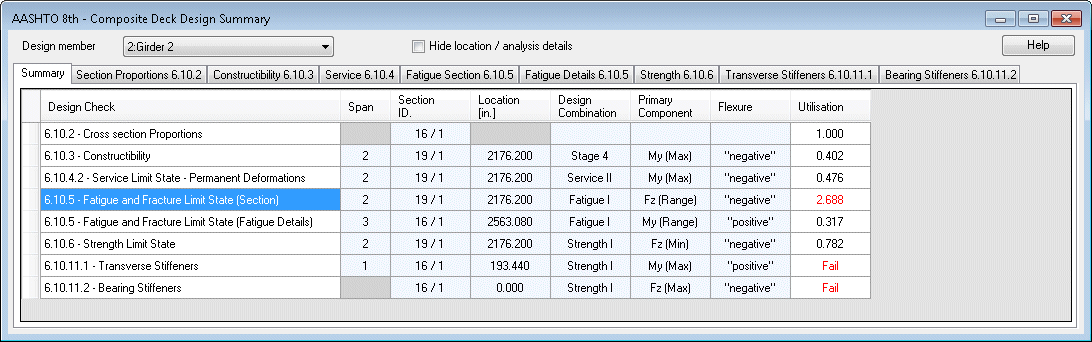
Steel Frame
Design improvements
The Steel
Frame Design software option
now supports
- ANSI/AISC 360-16 Specification for Structural Steel
Buildings, American Institute of Steel Construction, Chicago, July
2016
- GB50017-2017 Standard for design
of steel structures, China Architecture & Building Press, China.
Reinforced Concrete
Frame Design improvements
The RC Frame
Design software option now
supports:
- AASHTO 8th Ed. (USA)
- AS5100.5-2017
(Australia)
- CSA S6-14 (Canada)
- IRC:112-2011 (India)
Reinforced Concrete
Slab/Wall Design improvements
The reinforced concrete slab/wall design
facility now supports:
- GB
50010-2010 Code for design of concrete structures, China
Architecture & Building Press, Beijing.
Vehicle load optimisation
enhancements
The Vehicle Load Optimisation
software option now supports:
- India IRC:6-2017 Standard Specifications and Code of
Practice for Road Bridges - Section : II - Loads and Stresses (7th
Revision) Indian Roads Congress, New Delhi.
Geotechnical
Additional K0
models
Two additional K0
initialisation options, 'Wroth' and 'OCR sin(phi)', have been added to
the Modified Cam Clay material model to allow initial stresses in soil
to be calculated.
Phi-c reduction
Phi-c reduction
attributes can now be defined and assigned to a model to assess soil
stability and safety factors for soil that is represented by
Mohr-Coulomb or Hoek-Brown material models. Attributes can be assigned
to all or just some of the relevant features in a model, allowing the
safety of a particular slope (for example) in a large analysis to be
evaluated without other parts of the model being affected. Assignment
is made to a particular loadcase or analysis stage, which defines the
applicable loading, boundary conditions and activation status.
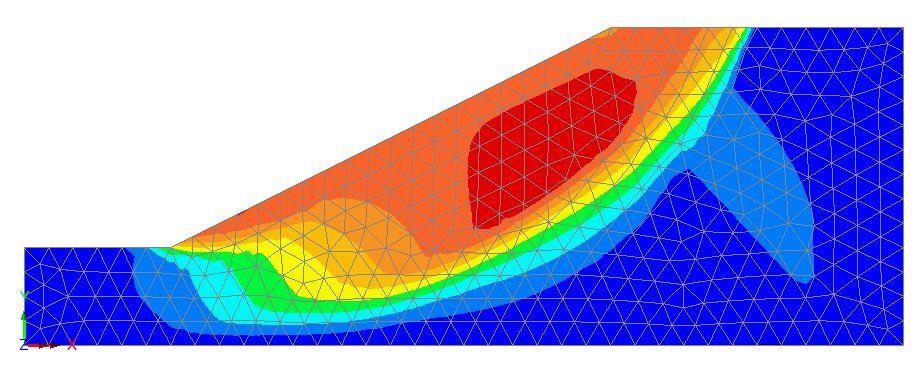
By its very nature, a phi-c reduction
analysis will always run until solution failure, so it is best used in
branched analyses where it can be used to study safety factors at
several stages of construction without terminating the solution.
Drained and
undrained conditions
Drained and Undrained
attributes can be defined from the Attributes > Pore Water
Pressures... menu item. They are used to define regions of a model
where the soil is drained or undrained.
Drained and undrained
attributes can be assigned to features representing soil that are
meshed with two phase elements and modelled with two-phase materials
in both 2D or 3D models. The use of such attributes is a conceptual
shortcut from the beginning to the end of a consolidation analysis,
representing the extreme undrained and drained conditions.
Hoek-Brown material
model
The Hoek-Brown model
is now supported. This is an elastic-perfectly-plastic constitutive
model suitable for the modelling of rock failure. It is an empirical
model, and its parameters are based on both laboratory test data, and
visual observation of the rock. The model can be used with standard
continuum elements as well as the two-phase elements.
General modelling, material and results
enhancements
Bridge Deck
(Grillage) attributes introduced
Bridge Deck (Grillage) geometric
attributes have been introduced to define geometric properties of
specific types of bridge decks that are analysed with reference to, or
derived from grillage formulae published by Hambly and others.
When assigned to a model along with a
new Bridge Deck (Grillage) material attribute, which contains separate
material definitions for the slab, girders, slab and reinforcement
(for cracked sections) that are defined in the relevant Bridge Deck
(Grillage) geometric attribute, users can more easily analyse the
different phases of construction of these types of bridge decks with
one model by the use of the multiple analysis facility. In short, one
set of grillage geometric attributes is suitable for the life of a
bridge, as the sections do not change, whereas several material
attributes may be needed to represent the in-construction, short term,
and long term cases.
Bridge deck temperature
and shrinkage profile loading
Bridge deck temperature profile loading
can be defined for the following design codes.
- AASHTO 8th
- AS 5100.2:2017
- EN1991-1-5:2003
Approach 1
- EN1991-1-5:2003
Approach 2
Bridge deck shrinkage profile loading
currently supports:
General
variation of temperature or strain through-section
For general use, a temperature/strain
profile loading can be defined by stating the temperature of the top
of the section followed by defining a series of segment thicknesses
and corresponding values for the specific height at which the
expression is being evaluated. Segment thicknesses and
temperature/strain may be stated as a single value, or as expressions,
making it possible to replicate expressions in bridge industry Codes
of Practice and define code-specific profiles that are not currently
supported elsewhere in LUSAS.
Defined profiles can be visualised for
a stated visualisation height. The same profile may be assigned to
multiple geometric sections of differing heights.
Generate
influences from beam/shell resultants and inspection locations
Direct Method
Influences can now be generated from beam/shell slice resultant
locations and at inspection locations. Direct Method Influence
attributes can be assigned to pre-defined Inspection locations, or to Beam/Shell
Slices using the 'Assign to' context menu item for the DMI attribute,
and then selecting the inspection points or beam/shell slices to which
the assignment should be made on the Influence Assignment dialog that
subsequently appears.
The ability to assign
DMI attributes to Beam/Shell Slices now makes it possible to use the
Vehicle Load optimisation facility on bridge decks idealised using
mixed beam and shell elements.
Model view
"Orientation cube" introduced
An orientation cube can now be
optionally displayed in each model view window. This provides
visual feedback on the orientation of a model, and rotates and
updates as the model is rotated or orientated. The top of the
cube is aligned to the defined vertical axis for the model.
The orientation cube has
labelled faces with default names of Left, Right, Bottom, Top,
Back and Front, and edges and corners that highlight when a
cursor is moved over them. Selecting a face, edge or corner of
the cube will orientate the model to be viewed from the
selected direction. The model can also be dynamically rotated
by clicking and dragging to rotate the orientation cube.
Home, Dynamic Rotation, Resize,
and Perspective buttons can be optionally added beneath the
axis cube for easy selection.
|
Branched
analysis introduced
Analysis
branches may be added to the Analyses
Treeview by selecting the New > Branch context menu
item for any loadcase in the Analyses
Treeview that has (or inherits) a nonlinear or transient
control. They allow the creation and solution of one or more
sub-analyses to investigate the response of the model at a
particular loadcase or "stage".
Examples of
use include:
- Carrying
out a linear moving load analysis of construction
equipment during each stage of the construction of a
segmental bridge deck,
- Performing
an eigenvalue natural frequency analysis or a buckling
analysis during construction.
- Performing
a phi-c reduction analysis to derive safety factors for a
geotechnical model from each stage in an excavation
process.
- Performing
an earthquake analysis where gravity is applied in a
static nonlinear step, then the earthquake is run as a
transient branch. Several sample earthquakes may be run in
each branch.
Any number of
sub-analyses may be defined for a single parent loadcase. |
Access to Fastest
available and Frontal Solvers provided
The Fast Multi-frontal solver is now
made available by default to new clients.
Two Solver-related radio buttons
previously included at the bottom of the 'Model properties' dialog
have been replaced with a droplist control on the dialog that
additionally allows specifying solution options on the 'Solve Now'
dialog. These now allow for solving by the fastest available and
appropriate solver for the task in hand, or the frontal solver, which
provides more error diagnostics should issues arise. An option to only
solve for the first loadcase (for quick model attribute assignment
checking purposes) is also included.
Direct method
Influence analysis improvements
Direct Method Influence analysis is now faster
because the Solver results file is now generated at the same time as
the stress recovery stage, saving significant processing time.
Larger Direct Method Influence analyses
can now be carried out with either a finer grid or a finer mesh
without manually setting any additional parameters. The analysis is
split into batches that make maximum utilisation of the memory
available but which ensure that no matter how large the DMI analysis,
it will solve successfully.
Rail Track Analysis
enhancements
The LUSAS Rail Track Analysis software
option now includes the following new features / enhancements:
- Bearings
can now be modelled offset (inboard) from the ends of the decks.
- Multiple
Train Loading Groups can be analysed within the same analysis.
- Avoidance
of stubby elements in the modelling.
- Improved
pier modelling.
- Train
loads are allowed to be outside the extents of the model. This
allows long trains to be passed over structures without having to
have excessively large embankments to model the correct arrival
and departure of the trainset from the structure.
- Use it
for EuroCode nomenclature of Traction loads (instead of
Acceleration).
- Significant
speed up of train/rail load definition and assignment.
- Section
axes for deck and pier now included in the Geometric Properties
worksheet.
- Improved
results / chart titles in the tabulated output.
Slice resultants
improvements
Once defined,
slice sections are now visualised immediately on the model without the
need for a solve to have taken place first.
Results
averaging speed-up
Averaging of element results across
discontinuities has been made more efficient, reducing the time it
takes to display averaged results in this situation.
General
User change requests
In addition to the range of new
facilities and improvements listed, many user change requests have
also been implemented. The originators of all requested changes to the
software (some of which are included in the above list of
enhancements) that have been incorporated in this release will be
notified individually.
Documentation
All online and printed documentation
has been updated for this new release. Manuals are provided in PDF
format as part of any LUSAS installation, and are also available for
download from the LUSAS website.
New and Updated
Worked Examples
The following new and updated examples
illustrate some of the new facilities provided in this release.
Within LUSAS, see Online help >
Worked Examples > For LUSAS Bridge and LUSAS Civil &
Structural for details.
Other
worked examples
All existing worked examples
have been updated to match changes made to the software.
Individual worked examples in
PDF format are provided as part of the LUSAS software download file or
release DVD, and are also available from the online help. Examples are
also available from the LUSAS User Area.
Other
Potential issues
opening PDF files referenced in CHM files
On some PCs, and for certain operating systems,
the installation of security updates as released by Microsoft can
affect the opening of PDF files from the table of contents panel
within the CHM file-based help. Any links to PDF files from within
help topic pages may similarly be affected.
If problems are found when
attempting to open these files from within the online CHM file
supplied please note the following:
- Selected manuals
are supplied in PDF format on the installation kit and these are
normally installed into the <LUSAS Installation
Folder>/Programs/PDF_Manuals folder.
- Workarounds/solutions
may be provided by Microsoft during the availability and support
of this particular LUSAS software release.
Previous new facilities and improvements in
this release
None, this is the first
release of Version 19.
|