User Area > Advice
Rules for connecting elements
General
| Degrees Of Freedom For Elements
| Guidelines For Nodal Connectivity
| Recommended Element Connectivity
A finite element analysis consists of solving a set
of simultaneous (equilibrium) equations which relate structural
displacement, stiffness and force. In LUSAS, the force and stiffness
terms are evaluated from user information and the displacements are
the unknown values. The equation solved is:
f = K a
Where f are the forces, K the stiffnesses and
a
the displacements. A similar idea applies in field analyses in which
potential rather than displacement is the unknown variable.
For structural analyses the displacement at a node
will, in general, consist of translational and/or rotational
behaviour. Each of these displacement components are termed degrees
of freedom. In general three dimensional space there are a
maximum of six independent degrees of freedom which are
u, v, w translations
corresponding to displacements in the x, y, z axis directions
respectively
qx, qy,
qz
rotations corresponding to rotations about the x, y,
z axes respectively
For field analyses there is only one degree of
freedom called the potential (F)
for all spatial dimensions. That is, one, two and three dimensional
field elements each have just the one degree of freedom at each
node.
Apart from the obvious distinction between structural and field
analyses, the number of degrees of freedom at a node depends upon
the element type. It is also governed for some elements by whether
the node is positioned at the corner or the midside of the element.
The Rules...
Element nodes from different element types may be
connected according to the following general rules
-
For the element node having fewer number of
degrees of freedom, these must be in the same order and of the
same type as the other connecting element node (for nodes with
equal numbers of degrees of freedom the selection is
immaterial). For example connecting a GRIL element node (w, qz,
qy)
and a BEAM node (u, v, qz)
is not applicable because the order and type are dissimilar.
Connection between an HX8 (u, v, w) and a QSI4 element (u, v, w,
qx, qy, qz)
is possible since the first three freedoms are of the same type
and order
-
Elements having different spatial dimensions
(1D, 2D, etc) must not be connected together. For example a BEAM
element (2D) and a HX8 element (3D) would be an inappropriate
selection
-
Structural and field elements must not be used
together at any time
-
The stress types for the connected element nodes
need to be compatible. For example, although the degrees of
freedom for plane stress and plane strain elements are both
identical (u, v), the assumptions made for the stress
calculations are totally different and render them incompatible.
Similarly, a beam and an axisymmetric element are entirely
incompatible
-
For integral element connection (full
connection along an element length/edge), matching of the number
of nodes of the elements is crucial.
-
The diagram (a) below shows
a correct connection in which a two-noded line element is
integrally joined to a four-noded surface element - also having
two nodes along each side.
-
Example (b) violates this rule
because the line element does not have a corresponding midside
node with which to provide mutual connectivity. This would
result in a warning, and where possible (within the limits
imposed by the other rules), constraint equations would
automatically be used to constrain the midside node to the
corner nodes as a work around.
-
Diagram (c) is
included to illustrate single point connection at nodes.
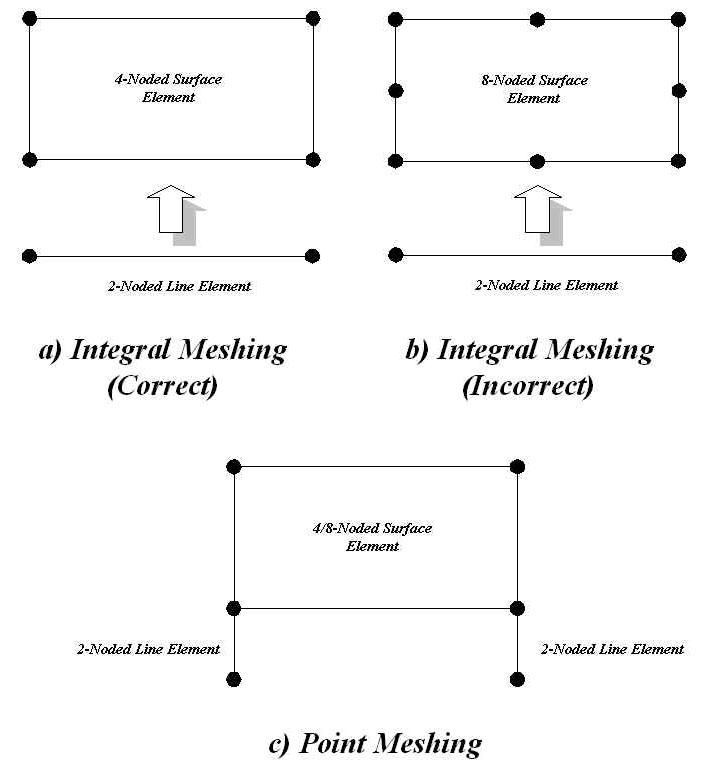
Degrees Of Freedom For Elements
The Element Reference
Manual provides details of all the elements available in LUSAS and
provides the degrees of freedom for each. There are summary
tables for each general element grouping at the beginning of the
manual which allow for quick comparison between different elements
within the same group or of the same type.
Help > Help
Topics > Contents > Element Reference Manual > Element
Summary Tables
Guidelines For Nodal Connectivity
Integral connection as
illustrated above, automatically means that single point
connectivity will be possible. However, there are some cases
where single point connectivity alone may be possible. This
can be established from checking corner/end nodal freedoms for the
elements to be used together in the Element Reference Manual as well
as the Notes regarding use. With regards to the choice of
joint element to use with other elements, there is a section in the
Element Reference Manual that gives a table for checking joint
compatibility to facilitate the selection of a suitable joint
element to use.
Help > Help Topics >
Contents > Element Reference Manual > Appendix L : Joint
Element Compatibility
Recommended Element Connectivity
The following tables are the recommended element
choices when connecting plates or shells integrally with beam
elements.
Element Type4 |
Element Name |
Integrally
Connected Beam Element Options |
Single
Point Connected Beam Element |
Notes |
Thin Plate |
QF4, TF3
QF8, TF6
|
GRIL
Not Available
|
GRIL |
Linear analyses only |
Thick Plate |
QSC45
QTF8, TTF6 |
GRIL
Not Available |
GRIL |
Linear analyses only |
Thin Shell |
QSI4, TS3
QSL8, TSL6
|
BMI211,
BMI22, BMS32,3, BTS33
BSL3, BSL4 |
(BMI211, BMI22,
BMI31, BMI33, BMS32,3, BTS33)6 |
Nonlinear analyses available with the semiloof shell and
beam element combination |
Thick Shell |
QTS4, TTS3
QTS8, TTS6 |
BMI211,
BMI22, BMS33, BTS33
BMI311, BMI33 |
BMI211, BMI22,
BMI31, BMI33, BMS32,3, BTS33 |
Nonlinear analyses available except for BMS3 element |
Notes
-
This thick
beam is recommended.
-
For thin analyses requiring both
quadrilateral and triangular elements, this beam is recommended
-
The linear and
quadratic 3D Thick Beams (BMI21,22,31,33) have nonlinear
capabilities and really combine what 3D Thick Beam (BMS3) and 3D Thick Beam (nonlinear), BTS3 can do individually and effectively supersede both.
-
The difference between a thin and thick plate or
shell element is in the evaluation of through-thickness shear
deformation. Thick elements take this effect into account
while thin elements do not. Shear deformations, however,
would only be of significance in relatively thick sections
(refer to any good structural design book for further
information). Note that shear deformation is different from
shear stress. Shear stress is applicable to both thin and thick
elements (varying according to the classical equation dM/dx).
However, although through-thickness shear stresses are present
in thin elements implicitly, they are not required in the
element formulation and, hence, are not evaluated or output
-
There are no associated triangular elements
available with this element
-
These thick
beam options for single point connectivity to quadratic order,
Semiloof thin shells (QSL8, TSL6) at corner nodes only
provides translationally connectivity (pinned connection) only.
|