Case Study
Support
Hinge Assemblies for the Gateshead Millennium Bridge
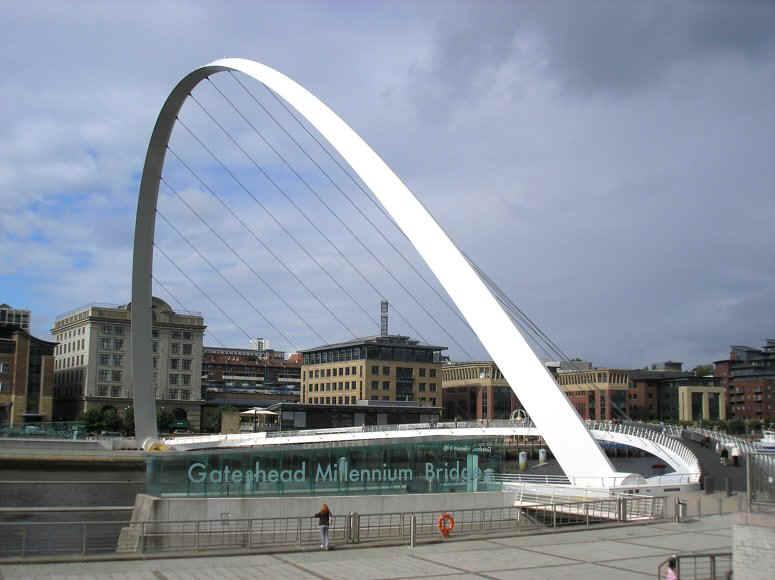
The Gateshead Millennium Bridge,
designed by consulting engineers Gifford and Partners (now part of Ramboll) with
architects Wilkinson Eyre, is an eye-catching, steel, opening bridge that spans
105m across the River Tyne in Newcastle, UK. When closed, small river craft can sail beneath the bridge
but, for larger vessels, the cable-stayed double arched structure pivots at the abutments
through an angle of 40 degrees to give a 25 metre high navigational clearance. Kvaerner Markham Engineering, based in Sheffield,
designed the electro-hydraulic actuation and control systems on the bridge and used LUSAS Analyst
to design the support hinge assemblies which withstand the large axial and radial thrusts
that are produced.
At each end of the bridge, the
deck and arch converge onto the support hinge assembly. This comprises a cylindrical shaft
which is supported at either end by a support bearing. The bearings in turn sit in 3.67m
long x 1.1m wide x 1.67m high cast steel pedestals that each weigh in the order of 14
tonnes. Each pedestal is bolted to the concrete substructure and withstands maximum design
loads of approximately 4000kN vertically, 7700kN in the plane of the bolts, and 4200kN
transversely. To open the bridge, a bank of hydraulic rams push against a steel paddle
attached to the cylindrical shaft and push the whole structure through the required
opening angle. Cylinder mountings for these rams, each weighing approximately 2
tonnes,
were also designed using LUSAS.
The cast steel pedestals were modelled using 8-noded solid elements. In
a series of 3D solid static analysis assessments, various loadcases and support conditions
were defined in order to assess the stresses in the cast steel pedestals, the contact
stresses in the concrete, and to ascertain reaction forces at bolt positions for the
various casting designs.
|
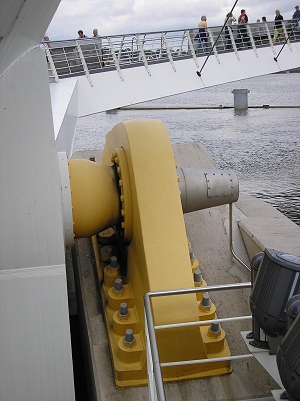
|
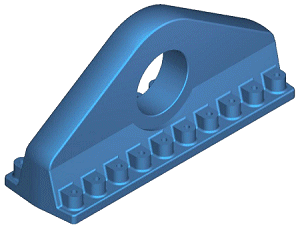
|
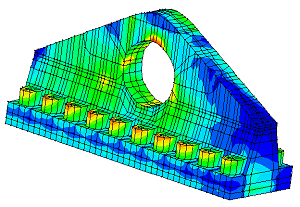
|
Phil
Snowsill, Kvaerner Markham's Senior Design Engineer on this
project said, "We had fairly high loads coming onto quite compact components. This,
with the additional requirement that all components had to be aesthetically designed
rather than being just the simplest or most efficient shape meant that LUSAS was ideal for
the job. With LUSAS, we optimised the distribution of material to give the minimum weight
and cost for the applied loading and got more accurate answers than we would have done by
other means."
Read about the design of the bridge
structure
"With LUSAS, we optimised the distribution of material to give the minimum weight
and cost for the applied loading and got more accurate answers than we would have done by
other means."
Phil Snowsill, Senior Design Engineer, Kvaerner
Markham
Other LUSAS Analyst case
studies:
|
|
Software Information
|