User Area
> Advice
Using joints: Material attributes
Using Joints: Mesh
| Geometric
attributes | Material
attributes | Spring
stiffnesses | Supports
| Loadcase properties
The joint material attribute used in your model controls
how the joint will behave when subjected to loading or
displacements etc. There is a comprehensive selection of joint
material available (listed below), appropriate for a wide
range of common uses:
Linear Joint Models
- Spring stiffness only corresponding to each local freedom. These local directions are defined for each joint element in the Element Reference Manual.
- General Properties advanced specification of joint properties of spring stiffness, mass, coefficient of linear expansion and damping factor.
Nonlinear Joint Models
- Elasto-Plastic (Tension and compression equal) with isotropic hardening and equal tension and compression yield conditions.
- Elasto-Plastic (Tension and compression unequal) with isotropic hardening and unequal tension and compression yield conditions.
- Smooth Contact with an initial gap.
- Frictional Contact with an initial gap. Friction contact joints can be specified to permit lift-off in a user-defined direction.
- Trilinear Earth Pressure creates a piecewise linear joint material whose properties vary with depth, such as those used to represent a layer or stratum in a
soil-structure interaction or geotechnical analysis.
- Piecewise Linear, Elastic allows a single force/displacement (moment/rotation) curve to be defined for each freedom by defining a number of line (curve) segments.
- Piecewise Linear, Elastic (Axial Force Dependent) Allows any number of force/displacement (moment/rotation) curves representing the behaviour under different axial forces.
- Piecewise Linear, Hysteretic A range of inelastic hysteretic joint models for basic and complex hysteresis.
- Non-interacting Pushover Hinge material models the development of pushover hinges in members where failure is dominated by a single action; for example bracing members subject to axial forces, beam members in the floor of a building subject to seismic loading or shear in columns in which axial force can be ignored.
- Interacting Pushover Hinge (PMM) material models the development of pushover hinges considering the interaction of axial force and biaxial bending.
- Nonlinear user-defined A user-defined joint model. This allows user-supplied joint property subroutines to be used from within LUSAS. This facility provides controlled access to the pre- and post-solution constitutive processing and nonlinear state variable output via these user-supplied subroutines.
Seismic Isolator Joint Models
- Viscous dampers - Kelvin and Four Parameter Solid modules available.
- Lead Rubber Bearings with plastic yield and biaxial hysteric behaviour.
- Friction Pendulum System with pressure and velocity dependent friction coefficient and biaxial hysteretic behaviour.
Full information on all available
joint materials is given in the help menu:
Help > Help Topics >
Contents > Theory Manual Volume 1 > Chapter 4 Constitutive
models > 4.12 Joint Models
The orientation of your joint
mesh elements, usually controlled using local coordinate
attributes, is crucial.
Example Use: Lift Off or Tension-Only
Joint Materials
Whilst lift-off/contact supports can be
easily modelled in either a linear or nonlinear analysis, simply
by choosing the "Lift-off" option for a particular
freedom in a defined support attribute, and whilst for modelling
tension-only cables there is a tension-only bar material for the
purpose, there are cases where simple lift-off/contact between mesh
is required or more control over the behaviour is desired/required
and therefore a joint mesh may defined and used
instead.
There are generally three alternative material attributes applicable: "elasto-plastic",
"frictional contact" or "smooth contact" for
modelling contact and lift-off behaviour.
The latter is recommended for simple contact problems where friction
is not modelled because the input is straightforward and because it
strains elastically and therefore allows the joint to go in and
out of contact through different analysis stages recoverably,
without accumulating and retaining any plastic strains.
Attributes > Material > Joint... >
pick "Smooth
contact"
For simple contact the "lift-off force" should be zero.
The "mass" would also be zero because in this case the
joint represents merely the contact interface between other
features. Where features are drawn and meshed to be initially in
contact, the "Initial gap" would also be entered as
zero. With the other two input rows, the user then has
control over the stiffness to be applied when there is contact
(zero or negative force in the joint) and when there is lift-off
(positive force in the joint) for each freedom. Often,
contact will be required in one direction only and so for the
other freedoms the value entered for contact and lift-off
stiffnesses will be equal - usually either both low/zero (free
lift-off and sliding contact) or both high (fully guided contact
and lift-off). Note however, that if ill-conditioning
warnings occur or convergence probelms
are experienced, high extremes of stiffness used should be
mitigated.
Similarly, the "Smooth
contact" joint can be used to model the opposite behaviour,
tension-only, whereby a high "lift-off stiffness" is
entered for positive force in the joint (tension) and a low/zero
stiffness is entered for the "Contact spring stiffness"
for negative force in the joint (compression).
The stiffness values entered and
the number of freedoms requiring input for this material will
depend on the joint element type chosen and the features that the
joint mesh and the associated material will be assigned to.
The different cases are descirbed for the more commonly used
element types and example structural arrangments illustrated
below.
Between
point features and at the ends of lines
The number of "Freedoms" specified in the material should match the DOF in
joint mesh attribute
selected.
- For a 2D beam model,
JPH3, Freedom=3 should be used:
the DOF are, in order, local x, y,
THz.
- For a 3D thick beam model,
JSH4, Freedom=6 should be used: the DOF are, in order, local x, y,
z, THx, THy, THz.
A stiffness value for the DOF in compression (input row 1 "contact") and tension
(input row 4, "lift-off
stiffness") is required.
Note that joints between
points can often be required at the ends of lines, for
example in a beam meshed model (see the images to the
right). In such cases, a joint can be quickly and
easily added to the end of a beam meshed line, by choosing
to include a joint via the "End Conditions"
settings in a Line Mesh attributed. The joint
material in this case would be defined as if it is to be
used for a joint between points, but assigned to a
selected line, choosing the option to "Assign to line
end(s)" when prompted.
|
|
Between line features
The number of "Freedoms" specified in the material should match the DOF in
joint mesh attribute
selected.
- For a 2D beam model,
JPH3, Freedom=3 should be used:
the DOF are, in order, local x, y,
THz.
- For a 2D grillage/plate model,
JF3, Freedom=3 should be used:
the DOF are, in order, local z, THx, THy.
- For a 3D thick beam/thick
shell model, For JSH4, Freedom=6 should be used: the DOF are, in order, local x, y,
z, THx, THy, THz.
- For a 3D thick beam/thick
shell model, For JNT4, Freedom=3 can also be
appropriate : the DOF are, in order, local x, y,
z.
- For a 3D solid model, JNT4, Freedom=3 should be used:
the DOF are, in order, local x, y, z.
A stiffness value per unit length for the DOF in compression (input row 1 "contact") and tension
(input row 4, "lift-off
stiffness") is required.
|

|
Between surface feature faces
The number of "Freedoms" specified in the material should match the DOF in
joint mesh attribute
selected.
- For a 3D thick shell model, JSH4,
Freedom=6 should be used: the DOF are, in order, local x, y,
z, THx, THy, THz.
- For a 3D solid model, JNT4,
Freedom=3 should be used:
the DOF are, in order, local x, y, z.
A stiffness value per unit area for the 3 DOF in compression (input row 1 "contact") and tension
(input row 4, "lift-off
stiffness") is required.
|
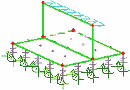
|
How
do I choose suitable stiffnesses for joint materials?
How do I model
lift off supports? (main page)
How
do I model tension only members? (main page)
How
do I model a hinged connection between shell meshed surfaces?
(main page)
|