- Time history seismic analysis
using lumped-mass stick (beam) models
- Static and peak seismic loading
application using shell models
- Coupled thermal-structural
analysis for spillage plus aftershock event using solid models
Costa Norte LNG Terminal, Panama.
LUSAS
Consultancy Services has extensive experience in carrying out a wide range of
analyses for large storage LNG tanks. Over the years its specialist
engineers have assisted
Korea
Gas Technology Corporation
(KOGAS-Tech) on various projects and analyses including, more recently,
the seismic isolation analysis of a 180,000m3
full-containment tank for the Costa Norte LNG Terminal project in Panama. On completion in 2018, it
became the first LNG reception terminal in Central America.
Overview
Panama and Central America are seismically active regions and LNG
tanks represent critical structures with stringent design
requirements under accidental and earthquake conditions. In this
context, base-isolation systems have become a cost-effective
solution to cater for increasing seismic demands in the design of
large storage tanks.
This
above-ground full containment tank comprises a 32.7m high, 9% nickel steel inner tank of
89m diameter - where the LNG is stored under
normal operating conditions - insulated from a 91m inside diameter post-tensioned
concrete outer tank intended to
contain any accidental spillage of LNG product. The base insulation sits on a concrete base slab
supported by 400 pedestal-mounted isolators, which are cast on top
of a reinforced concrete piled raft foundation. The overall tank
height to the top of the roof dome is 53.4m.
Analyses undertaken
LUSAS Consultancy
developed several finite element models to perform a detailed seismic assessment
of the LNG tank under different earthquake and accidental
conditions, including:
- Time history seismic analysis
using lumped-mass stick (beam) models
- Static and peak seismic loading
application using shell models
- Coupled thermal-structural
analysis for spillage plus aftershock event using solid models
Isolation system
Triple friction
pendulum bearing (TFPB) isolators were located under the tank
bottom slab in order to decouple the tank from the earthquake
ground motion and reduce the transmission of seismic energy to
the tank components.
In all, 400
pedestal-mounted TFPB were used, with 4 sliding concave
surfaces and 3 friction coefficients. These were modelled in
LUSAS using specialised joint materials which included
hysteretic damping and the variation of friction with sliding
velocity and normal pressure. As friction properties are
variable with time and also axial force, lower and upper bound
properties were used for the empty and full tank cases.
Under peak conditions, the
base-isolation was able to provide an overall effective damping of
up to 33%, with peak displacements of around 200mm, well within the
605mm bearing capacity.
|
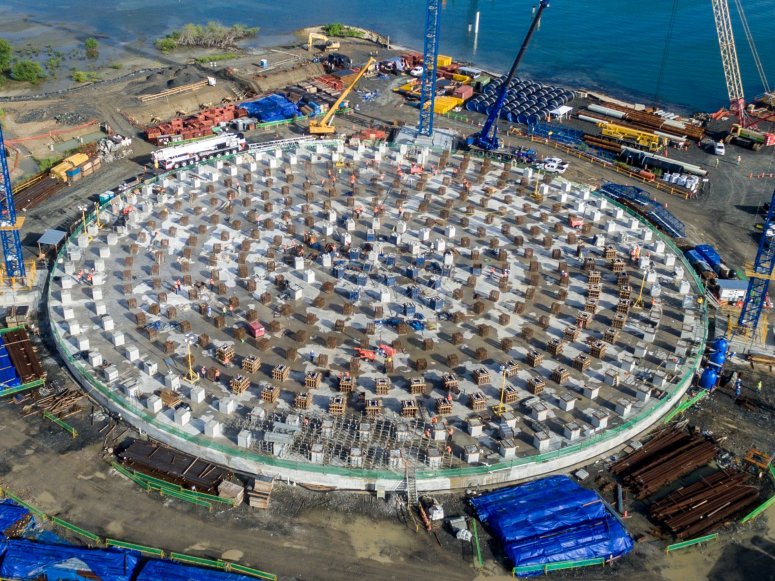
Installation
of base isolation system
(Image: AES Colon)
|
|
|
|
|
Isolator
force-displacement curve |
Acceleration-time
reponse in horizontal direction |
|
|
Soil-structure
interaction
The tank
foundation included a large number of closely spaced steel
piles, fully embedded in rock.
Piecewise linear joints
materials varying with depth were used in LUSAS to simulate
the nonlinear response of soil, including lateral bearing
capacity, skin friction and end bearing resistance.
Liquefaction
potential, cyclic loading, group effects and soil damping were
considered in the computation of the axial and lateral
stiffness of the soil support.
|
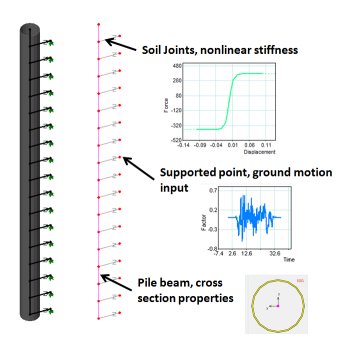
|
|
Pile modelling |
Time-history seismic
analyses
Lumped mass modelling
was used for fluid/structure interaction of the LNG and for
soil/structure interaction of the pile arrangement. The
nonlinear hysteretic behaviour of the isolation system required a
detailed dynamic analysis. Using nonlinear transient dynamic
analyses in LUSAS, time-history responses were obtained under
simultaneous horizontal and vertical ground motion.
Bedrock input motions of
0.33g (Operational Basis Earthquake) and 0.54g (Safe Shutdown
Earthquake) from the seismic hazard analysis provided by KOGAS-Tech were
used to develop multiple ground motion records to satisfy code
requirements.
The peak averaged results from the
dynamic analyses were combined with normal operation static loading
to perform a detailed stress analysis on a 3D shell model of the
structure.
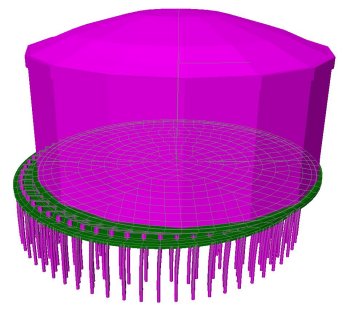
|
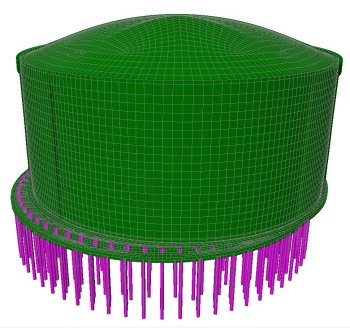
|
Lumped mass model
deformation |
Shell model
deformation |
|
|
|
Hoop
axial forces in shell model |
Spillage and
aftershock
A critical design
condition of LNG tanks is the aftershock (SSEaft)
event following an accidental spillage, which is assumed as a
result of a prior SSE earthquake that has damaged the inner
tank.
The aftershock earthquake was
estimated as 50% of the SSE, and the time-history analysis was
repeated on the lumped mass model considering that in this
case the LNG is in direct contact with the outer tank.
A 3D solid model
that included a state-of-the-art
nonlinear concrete material was developed to carry out a
semi-coupled steady state thermal analysis to assess the
effects of the spillage on the tank wall. Similarly, as for
the shell model, peak hydrodynamic pressures were subsequently
applied to the solid model and the liquid tightness and
collapse prevention of the concrete tank were assessed.
|
Solid model
deformation | Cracking / crushing | Compression zone
|
|
|
Spillage
temperature results and tank material modelling
|
In summary
Using the most advanced
finite element analysis/modelling techniques for isolated LNG tanks, LUSAS
Consultancy Services was able to provide KOGAS-Tech with a design basis
for the tank checks under OBE, SSE and SSEaft conditions;
including relevant results for foundation forces, isolator response,
freeboard, concrete tank forces, liquid tightness, crack widths, and
more.
"LUSAS has
provided us with a powerful design capability and advanced technical
support for over 20 years. On the Costa Norte LNG Terminal
project, the
use of LUSAS successfully verified our tank design for a highly
seismic region. With LUSAS, we can always ensure that our LNG tank
designs meet the strict design requirements of our clients."
Jung-Hoe
Kim, Civil & Arch Dept Manager, KOGAS-Tech.
Share this
article
Find out more
Other LUSAS Civil &
Structural case studies: