Case Study
Automated
track - structure interaction analysis
- Automated model building
and analysis from user-defined spreadsheet data
- Fast assessment
of track-structure interaction effects
- Evaluation of forces in
rails from thermal and in-service train loading
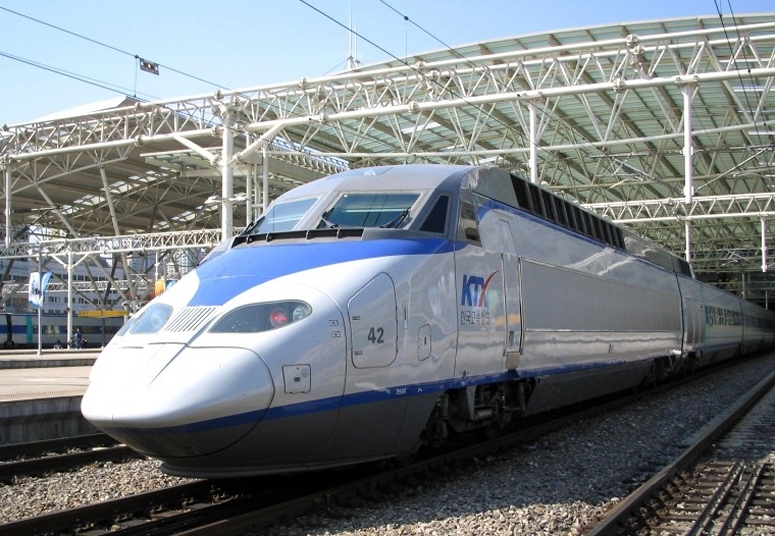
With a large percentage of track on
modern high speed railways comprising continuously welded rails
there is a requirement for accurate modelling of the interaction
of the track with respect to any supporting bridge structures, and
in particular, to calculate stresses and forces induced in the
track by both thermal and train loading. A LUSAS product
option, created initially for the Korea Railroad Technical Corporation (KRTC),
permits track-structure interaction analysis to the International
Union of Railways Code UIC 774-3. It allows KRTC to
automatically build models from data defined in MS Excel
spreadsheets, run an analysis, and quickly produce results in spreadsheet or LUSAS results file formats.
KRTC
KRTC is a subsidiary organization
of Korea National Railroad. It is involved with performing
planning, feasibility studies, design, and providing supervision
for major rail and high speed rail construction projects
throughout South Korea. Its stated aim is to enhance its
competitiveness by developing advanced railroad technology. By
using LUSAS Bridge to automate its track/bridge interaction
analysis it is achieving this to good effect.
Model building
KRTC’s track and bridge
interaction models are built automatically in LUSAS from
geometric, material property, and loading data defined in a
Microsoft Excel spreadsheet. Both thermal
loading to the track and train loading due to acceleration and
braking forces can defined. In accordance with the UIC774-3 code of
practice, a user-specified element length is used to define the
longitudinal embankment and bridge features. Rail clips, ballast
movement, bearings and pier stiffnesses are all included in the
analysis model. The model building dialogs allow for either one
train crossing one or more structures, or for multiple trains
crossing the same structure.
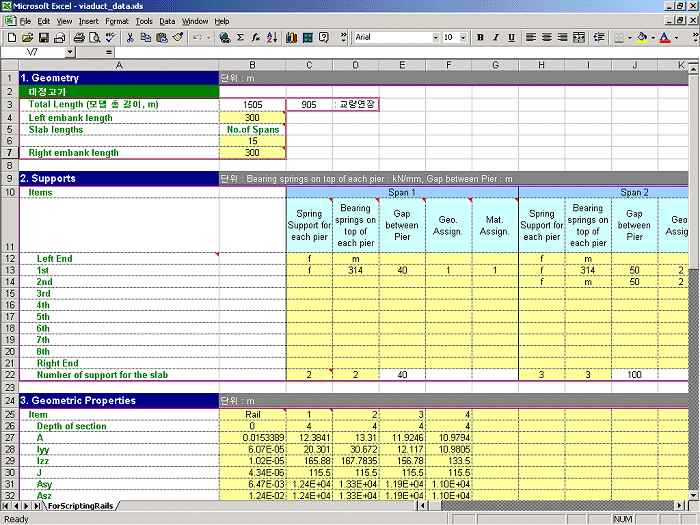
Spreadsheet
input data

Complete
embankment and viaduct model built by LUSAS
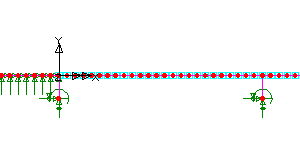
|
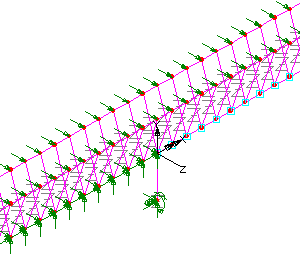
|
Enlarged view of
first span |
Exploded
isometric view of part of the model showing
embankment support
and the beginning of the first span |
|
Analysis and
results
When running an analysis, deck
temperature loading can be considered in isolation for subsequent
analysis of multiple rail configurations, or a full analysis can be
carried out considering the combined temperature in the deck and
rail loading. Because the response of the ballast and/or clips is
nonlinear a nonlinear analysis always needs to be carried out.
Results can be produced in either Excel spreadsheet or standard
LUSAS results file format. User-defined load combinations can be
specified. Spreadsheet results include axial forces in the rails for
deriving in-service stresses and forces and moments in the deck
structure.

|
Typical axial force results plot from LUSAS showing force in
continually welded rails from temperature loading to the deck
|
For multi-span and
multi-deck structures such as that shown above the interaction between
the embankments / abutments and other decks means that the behaviour
can be complex. As an example, when considering only thermal loading
on a structure having continually welded track it is common to see a
reversal of the axial force / stress in the rails.
Whilst not apparent from
the size of the model shown, the structure illustrated above is 325m
long and consists of two decks, each with two 25 m spans followed by
three decks, each with three 25 m spans. One pier / bearing support
for each deck is represented by a restraining spring which takes
account of the deflection characteristics of the pier / bearing system
in accordance with UIC774-3. All of the remaining piers / bearing
supports are roller supports allowing longitudinal movement of the
decks. Under the effect of temperature on the structure the axial
force / stress in either of the tracks / rails can be seen to vary,
primarily due to the interaction between the movable and fixed
structural components.
Find out more
Other LUSAS Bridge case studies:
|
|
Software Information
|