Case Study
Wichita's
Riverfront Footbridges
-
Staged
erection engineering analysis of two post-tensioned bridges across the
Arkansas and Little Arkansas rivers
-
3D linear
and nonlinear analysis
-
Cable
tensioning optimized giving reduction in
contractor's build time
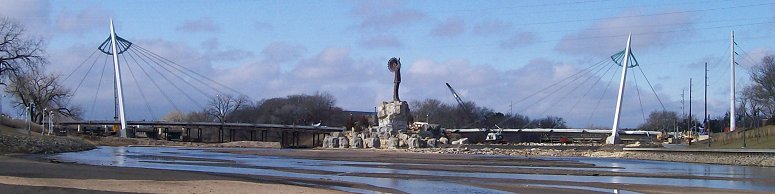
As part of Wichita's
riverfront development program, two cable-stayed pedestrian
bridges are being constructed to extend the city's cycle network
and provide better access to the surrounding neighborhoods and
business attractions. The bridges' contractor, Dondlinger &
Sons Construction Co., Inc., retained Genesis
Structures to analyze the staged erection process and
prepare the erection manuals required for each of these complex
cable-stayed bridge structures. Genesis Structures used LUSAS
Bridge analysis software to carry-out numerous detailed 3D linear
and nonlinear analyses of the bridges and their components to help
minimize the number of steps in the cable tensioning process and
reduce the Contractor's time and labor.
Overview
The
city of Wichita, Kansas, boasts a bike and pedestrian transportation
system that covers more than 150km, much of which runs through parks
and along its rivers. As part of its riverfront corridor improvement
project, two new bridges spanning 320 feet and 240 feet will
cross over the Arkansas and Little Arkansas Rivers respectively at the site of the
"Keeper of the Plains," a 45 foot high, raised, iconic Indian
statue. The bridges connect Exploration Place, a modern, interactive
science museum, with the culturally significant Mid-America All-Indian
Center. Because of their location, the cable-stayed bridges
incorporate tapered towers and a unique stay-cable configuration that
mimic feather shapes and other patterns found in Native American
headwear.
|
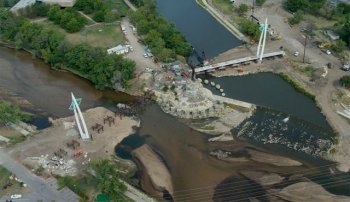
|
Bridge construction
Each bridge is comprised of a 120 foot
high steel tower of 60 inch triangular cross-section that supports
precast concrete box segments that are initially built on falsework
bents and then longitudinally post-tensioned together.
Each tower is
formed from two, 60 ton steel leg segments that are lifted into
position using a specially designed lifting saddle and integral
lifting lug. A 30 ton upper cable anchorage unit sits on the top of
both tower legs. This anchorage was assembled at ground level for ease
of installation of the bolted connections and then raised atop the
legs using special rigging. Adjustments were made using a screw jack
system to obtain the correct tower leg positions prior to final
assembly. Partial penetration welds around the full perimeter of the
upper ends of each leg and the unit secure it in place.
Decks are constructed of 32 foot long,
hollow box segments having a maximum depth at the bridge centerline of
48 inches and tapering to a 24 inch visible profile. During assembly
each segment is placed on steel falsework bents that allow
longitudinal movement of the segments during placement and
longitudinal post-tensioning. Ten inclined cable pairs support the
longer span bridge deck and eight cable pairs support the shorter
bridge. Main stay cables (provided by CBSI, Inc.) are 2 inches diameter with back stay cables of
3 3/8 inches diameter ASTM A586 Structural Strand.
Staged erection
analysis
Analysis with LUSAS was required to
model the complex erection sequence involving falsework construction
in the river, post-tensioning of the precast concrete deck system, and
sequential cable tensioning to lift the structure from its temporary
supports to create the free-spanning cable-stayed spans.
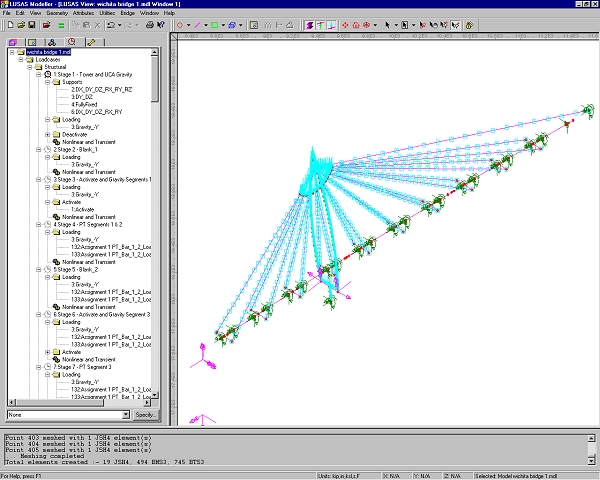
Project specifications required that
the bridge geometry be set-up at the beginning of its service life to
obtain the target geometry after 10 years of service. To accomplish
this, time-dependent effects due to creep and shrinkage in the
post-tensioned concrete deck segments had to be evaluated. This was
achieved by using the CEB-FIP 1990 creep and shrinkage material model
in LUSAS.
After
tower erection each of the 32 foot long deck box segments were
constructed upon structural steel falsework bents and initially
post-tensioned together for continuity using four, 1" diameter
post-tensioning bars. Following the complete longitudinal assembly of
the segments, four 19 strand, 0.6 inch diameter tendons were
installed and tensioned to obtain the required compression in the deck
system prior to cable installation. The LUSAS post-tensioning wizard
was used to model the erection of the deck segments at each stage of
the construction.
|
|
Preliminary tensioning of the stay
cables in the LUSAS model was accomplished through initial strain
loading of the nonlinear beam elements representing each cable. During
the actual stay-cable installation, the longitudinal concrete deck
system was to be lifted from its temporary supports through a
carefully planned installation sequence. The falsework system was
required to allow longitudinal movement and shortening of the deck
system as well as unrestrained lift-off from the supports. Modeling
for these effects was accomplished through the use of nonlinear joint
element supports in LUSAS. Final tensioning of the stay cables was
achieved by applying a negative temperature load to each cable pair to
obtain the desire tension. Excellent correlation was obtained between LUSAS
predicted cable tension values and on-site measurements.
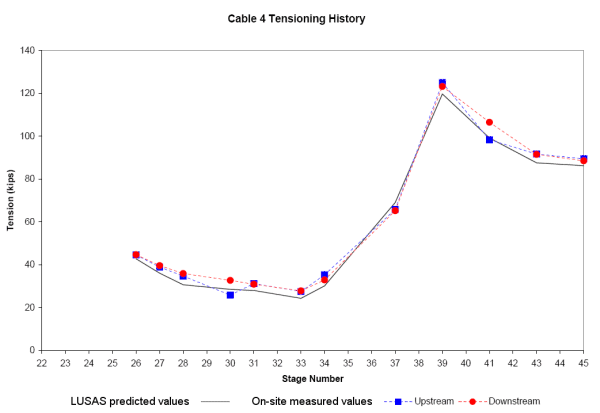
3D solid modelling of
box segments
Each
of the box segments contained access openings in the top slab to
provide access for the installation of the longitudinal
post-tensioning system as well as for two tuned mass dampers (provided
by Motioneering, Inc.) to control pedestrian-induced vibrations.
Openings for the tuned mass dampers exceeded 15 foot in length and
created areas of discontinuity in the top slab during lifting
operations and longitudinal post-tensioning. To verify that each of
these locations provided adequate continuity, individual segments were
modelled using 3D solid elements and checked for both lifting stresses
and longitudinal stresses due to post-tensioning.
|
|
3D
modelling of tower
The unique tower design of these
bridges creates a highly confined compression and flexural zone
immediately below the upper cable anchorage. To ensure adequate stress
transfer brought on by the cable tensioning, a 3D LUSAS model of the
entire tower and upper cable support was developed to determine the
local zone effects in this region. Confirmation of the local stresses
was obtained prior to proceeding with the complete analysis.
"We used LUSAS Bridge exclusively
for the erection engineering of the Wichita Bridges and obtained
excellent correlation between the on-site cable stayed measurements and the
values that LUSAS predicted for lift-off"
Dr. David Byers,
President, Genesis
Structures.
View
an animation of the staged erection engineering sequence
|
|
Find out more
Other LUSAS Bridge case studies:
|
|
Software Information
|